Seamless Feeding for Optimal Assembly Workflow
In the intricate world of catalytic converter assembly, substrate and shell feeding equipment takes center stage, ensuring substrates and shells are delivered efficiently and accurately to the production forefront. Proper feeding remains the cornerstone of uninterrupted, fluid operations across the production line.
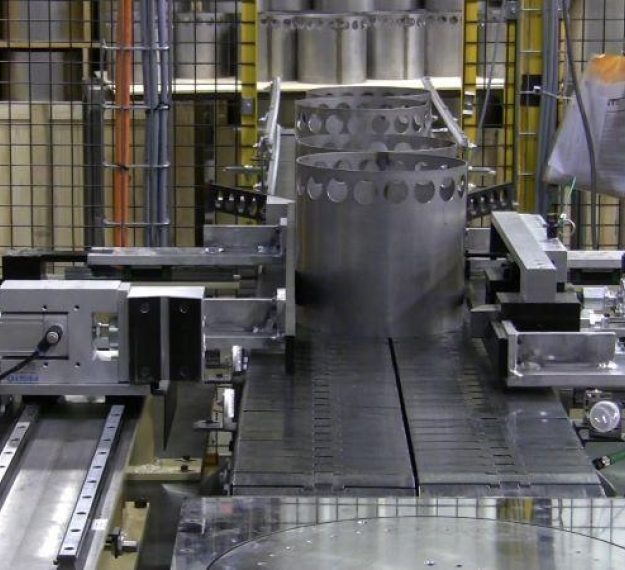
Compatibility: Feeding equipment should harmoniously handle various substrates (be it ceramic or metallic) and shells (whether stainless steel or alternative alloys) to accommodate diverse catalytic converter designs.
Speed & Efficiency: Minimize production hiccups. Equipment must swiftly and precisely transport substrates and shells to the assembly line, keeping any production lags or hitches at bay.
Automation: With automated feeding systems, expect a leap in production efficacy. Such equipment dials down manual errors and sidesteps hands-on interference. Integration with core assembly tools and other line equipment is vital for a frictionless workflow.
Flexibility: Changing production demands? No problem. Feeding tools should adapt effortlessly to an array of substrate and shell sizes, designs and even shifts in production volumes.
User Interface: An intuitive interface is paramount, allowing operators to set parameters, oversee the feeding procedure and capture results with ease.
Reliability: Consistency is the name of the game. Equipment designs should prioritize unwavering performance and curtail downtime, ensuring an unbroken material supply to the assembly line.
Safety First: Beyond functionality, safety is pivotal. Equipment needs inclusions like emergency stops and protective safeguards, keeping operators shielded from potential risks.
Maintenance & Calibration: Long-term efficiency demands regular check-ups and calibration. The design should provide straightforward access to essential components, streamlining maintenance endeavors.
Customization: Unique production demands might necessitate tailored solutions, making customization options essential for a perfect fit to specific assembly needs.
Cost-effectiveness: Striking the right balance between top-tier feeding efficiency, agility and automation, all while ensuring cost-effective ownership, is paramount. This not only considers the initial expense but also accounts for ongoing maintenance, calibration and potential equipment augmentations.
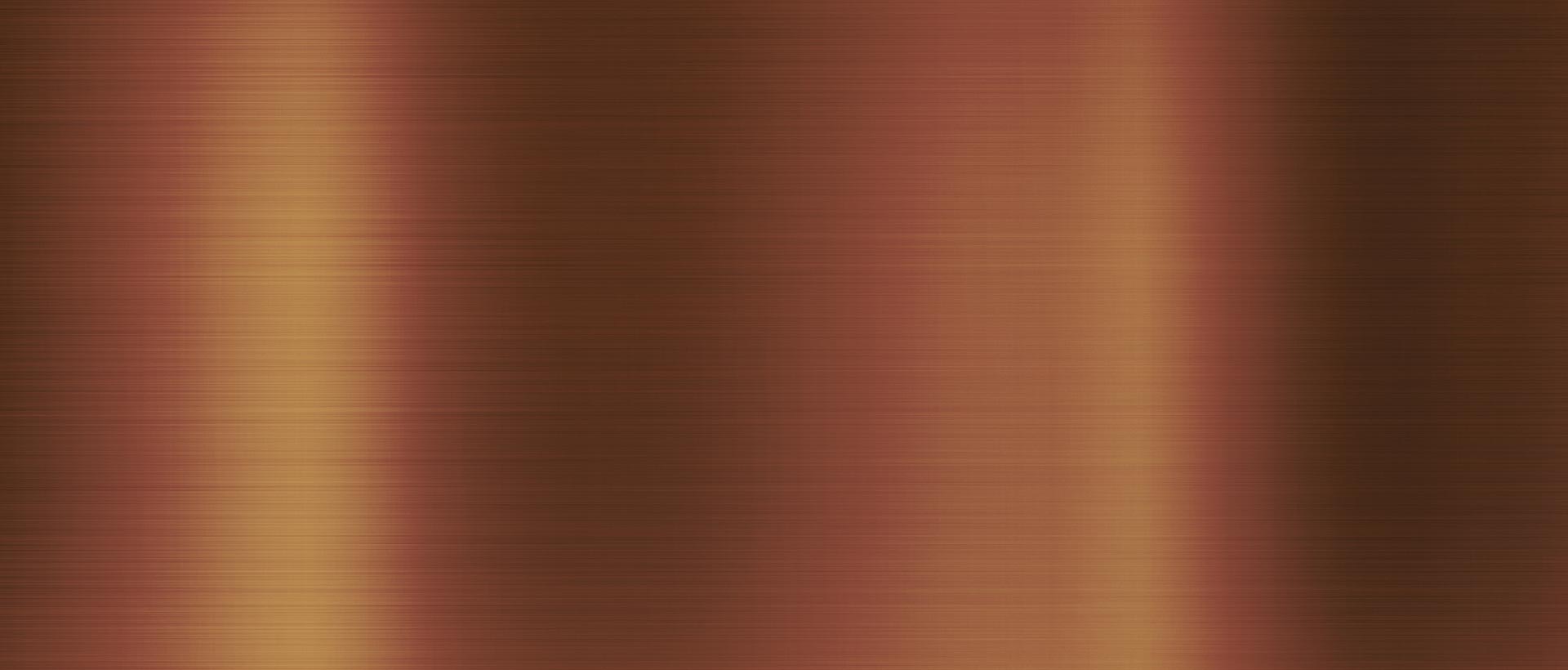
For unparalleled precision and efficiency in catalytic converter assembly, rely on AMT's state-of-the-art equipment.