Precision-Driven Pressing for Catalytic Converters
Substrate and shell press equipment stands at the heart of catalytic converter assembly. This essential gear guarantees that the substrate, wrapped snugly with its mat, aligns flawlessly within the shell. The correct press is pivotal in determining the converter’s structural soundness, enduring quality and peak performance.
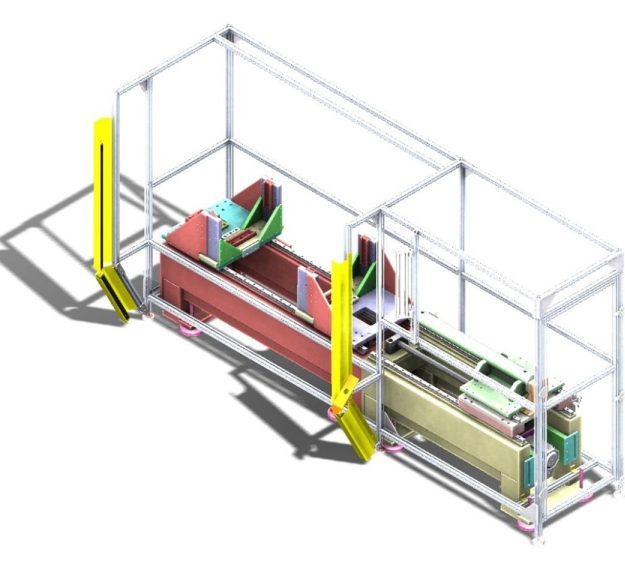
Precision: Achieving the precise pressure and even force distribution across substrate, shell and mat is a must, ensuring impeccable assembly and lasting durability.
Compatibility: Adaptable pressing equipment caters to varied types of catalytic converters, encompassing an array of substrate materials, shell types and designs.
Speed: For optimal production-line efficiency, swift pressing equipment is non-negotiable. It should rapidly execute its functions, evading any assembly process delays.
Automation: Modernized, automated pressing systems enhance production rates, curbing manual errors and slashing the need for hands-on intervention. Seamless operation demands integration with primary assembly devices and other production gear.
User Interface: An intuitive, user-friendly interface streamlines operations, enabling easy parameter input, pressing procedure monitoring and result tracking.
Adjustability: Adaptability is key. The equipment should allow tailoring to fit different substrate and shell dimensions and adapt to variable mat thicknesses and densities.
Data Insights: State-of-the-art pressing tools should come equipped with data acquisition and analysis capabilities. These features empower operators and engineers to spot trends, pinpoint concerns and fine-tune the production sequence.
Maintenance & Calibration: To preserve equipment accuracy and dependability, routine upkeep and calibration are paramount. Design considerations should prioritize easy access to vital components, simplifying maintenance.
Safety First: Safety-centric design is indispensable. Features such as emergency stops and protective measures safeguard operators from potential perils.
Customization: Unique catalytic converter assembly processes might call for specific equipment adjustments to fully cater to production needs.
Cost-effectiveness: An ideal balance between top-tier pressing capabilities, swift operation and automation is vital while ensuring the equipment is a sound financial investment. This encompasses the initial purchase expense and extends to future maintenance, calibrations and prospective enhancements.
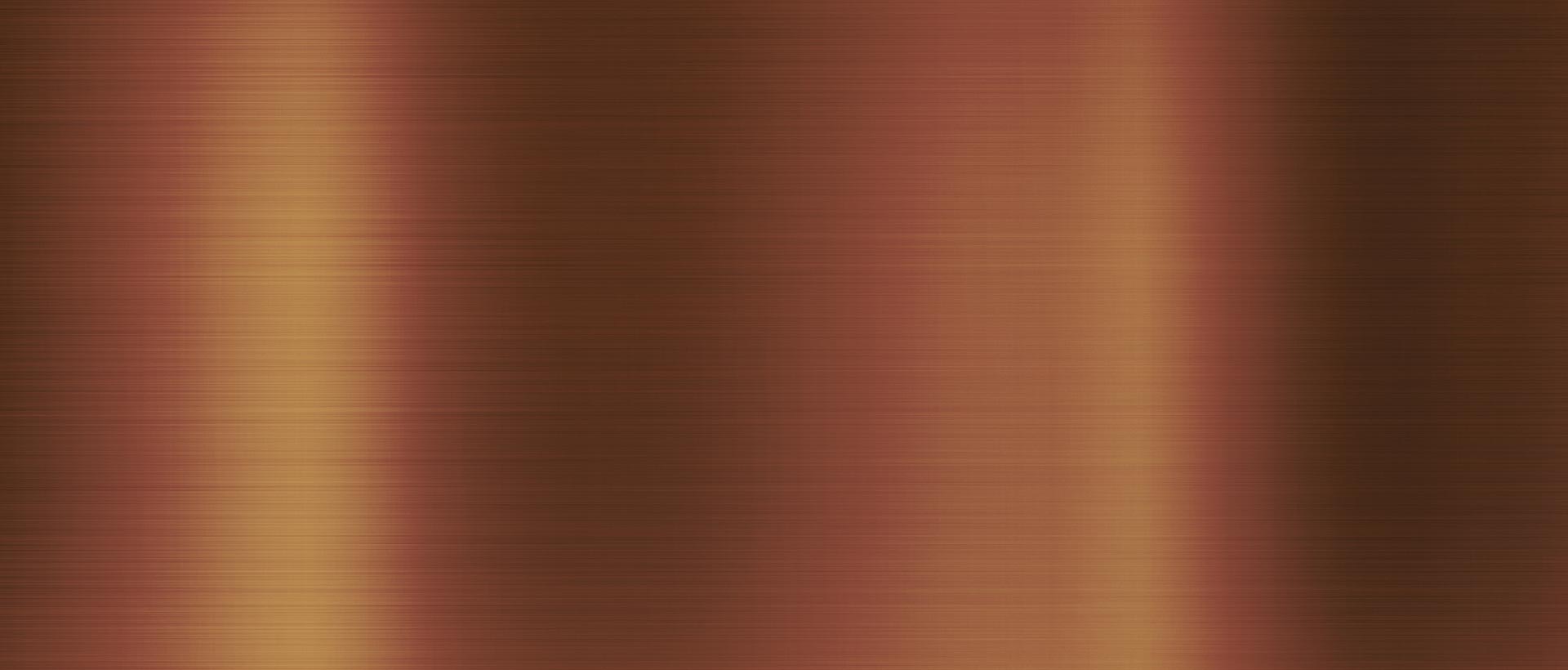
Elevate the precision and efficiency of your catalytic converter assembly. Lean on AMT's expertise and equipment.